Seikagaku steadily manufactures high-quality products at its two pharmaceutical manufacturing plants in Japan and endotoxin-detecting reagent manufacturing plant in the U.S. and plant related to CDMO business in Canada.
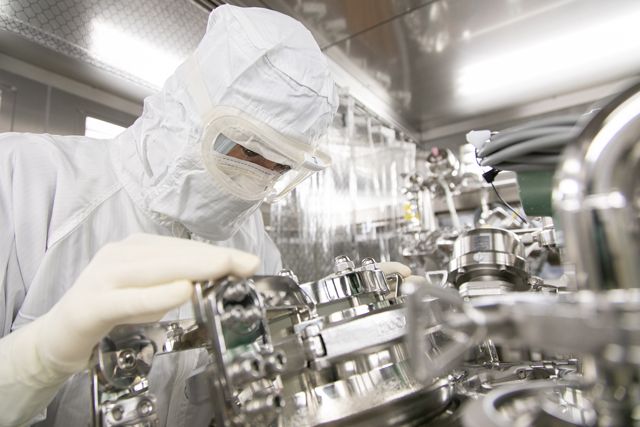
Companies that manufacture pharmaceuticals and medical devices must comply with the current regional regulations and engage in stable, continuous manufacturing. In order to deliver high-quality products to patients, Seikagaku complies with Good Manufacturing Practice (GMP) in Japan, the U.S., and Europe and strives for ever more rigorous manufacturing processes. Also, in the area of manufacturing control and quality control, we use computer systems to improve the completeness of records and are working to improve production efficiency through rigorous regular checks, elimination of human error, and improvement of manufacturing processes. We will continue to pursue continuous improvement and focus on the manufacture and supply of high-quality products that comply with global standards.
Providing a stable supply of products is an important mission of a pharmaceutical company. Seikagaku prepares against major disasters and other risks by diversifying raw materials suppliers and maintaining appropriate inventory levels. At the Takahagi Plant, which is responsible for manufacturing the finished products, we have introduced a quake-absorbing structure that reduces shaking for the main production buildings when an earthquake occurs. Through these measures, we have put in place a system capable of stable, reliable product production even in an emergency.
Furthermore, to cope with product supply risk from distribution network disruption following a disaster, we maintain a certain level of product inventory and have pharmaceutical product warehouses in two separate locations: within the Takahagi Plant in Takahagi City, Ibaraki Prefecture in the Kanto region and in Hirakata City, Osaka in the Kansai region.
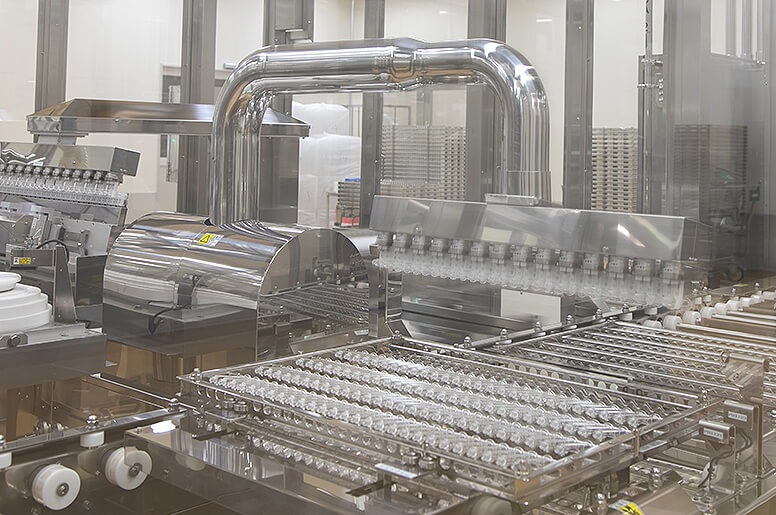
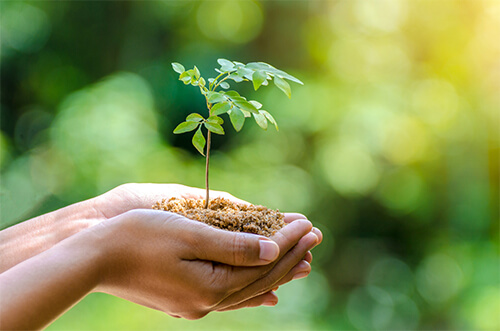
Keenly aware of the importance of protecting the global environment and the responsibilities associated with manufacturing activities, Seikagaku observes environment-related laws and regulations and voluntarily engages in environmentally friendly business activities.
We aim to balance environmental measures and business growth by continuing the energy-saving activities implemented heretofore and strengthening initiatives for efficient utilization of water resources, waste reduction and recycling, and other environmental improvements.
We have established the Energy Conservation Promotion Committee with the objective of promoting energy conservation activities and reducing CO2emissions and are managing energy use, implementing improvement measures for achieving energy use reduction targets established at each business site, and conducting energy conservation-related education and training. Furthermore, we have put in place a structure for increasing groupwide efficiency in which the Committee coordinates energy use and CO2 emissions volume and reduction measures each fiscal year, reports to the Management Committee, and discusses these matters. At the Takahagi Plant, the production site that uses the most energy, we have increased thermal efficiency and reduced CO2 emissions by updating boilers to convert boiler fuel from heavy fuel oil A to high-efficiency liquid natural gas (LNG). Furthermore, we have reduced energy use through initiatives such as conversion to LED lighting fixtures at production sites and laboratories and repairing and reinforcing steam pipes and steam traps. In this way, by continuously engaging in energy conservation activities groupwide, we have achieved our average energy reduction rate targets for the five years up to fiscal 2021.
The Takahagi Plant, located in northern Ibaraki Prefecture, is responsible for manufacturing finished pharmaceuticals and medical devices, including the joint function improvement agents that are Seikagaku’s mainstay products. When the plant opened in 1975, it had 28 employees. Since the launch of hyaluronic acid formulations in 1987, it has steadily expanded production scale as a manufacturing plant that specializes in injectable formulations. Today, the Takahagi Plant occupies a site of approximately 86,000 square meters and has five production buildings and some 200 employees.
The Takahagi Plant is responsible for manufacturing finished pharmaceuticals and medical devices, including the joint function improvement agents that are Seikagaku’s mainstay products. Today, the Takahagi Plant occupies a site of approximately 86,000 square meters and has five production buildings and some 200 employees.
The Takahagi Plant is one of the world’s largest manufacturing sites for hyaluronic acid pre-filled syringe formulations*, producing more than 25 million units per year for the Japanese and overseas markets. Sterility assurance is strictly required for the manufacture of injectable formulations, and the plant has minimized the risk of contamination by implementing unattended, automated manufacturing processes. The plant possesses facilities and equipment that can be adapted to optimal sterilization methods suited to the product characteristics.
*A kit with an injectable syringe that has been filled with solution.
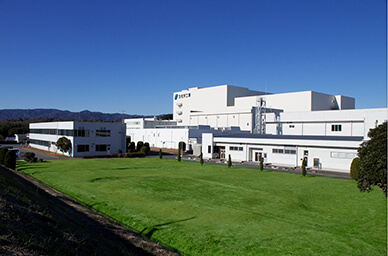
The Kurihama Plant, which manufactures bulk products, opened in 1947 and is Seikagaku’s most experienced plant. The plant has some 100 employees and manufactures high-purity hyaluronic acid and chondroitin sulfate for use mainly as active pharmaceutical ingredients.
The most important characteristic of the Kurihama Plant is that it specializes in the manufacturing of bulk products by extraction and fermentation. The plant applies advanced chondroitin sulfate extraction and fermentation technologies nurtured over many years since the founding of Seikagaku and has expertise in the efficient manufacture of high-purity bulk products from chicken combs, the raw material of hyaluronic acid, and shark cartilage, the raw material of chondroitin sulfate.
The Kurihama Plant is also responsible for some of the manufacturing processes for condoliase, the active pharmaceutical ingredient of HERNICORE, a treatment for lumbar disc herniation. The plant is currently preparing to start up new bulk condoliase manufacturing facilities to further strengthen the production scale.
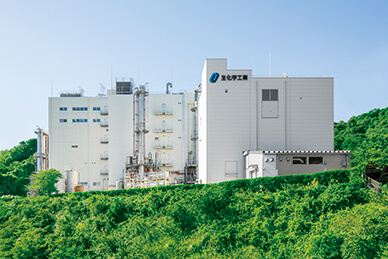
Associates of Cape Cod, Inc. (ACC), a wholly owned subsidiary of Seikagaku, was the first FDA-licensed LAL manufacturer in the world.It was established in 1974, became a Seikagaku subsidiary in 1997, and currently plays a central role in the global Bacterial Endotoxin Testing (BET) and clinical glucan detection sectors. ACC employs approximately 250 employees and has operations in the U.K. and Germany.
ACC’s reagent and diagnostics production facility, located at their campus in Falmouth Technology Park in Massachusetts, is vertically integrated with an end-to-end manufacturing operation that extends from harvesting horseshoe crab blood cells, a reagent raw material, to manufacturing, testing, packaging/labeling and distributing endotoxin and glucan in vitro diagnostic agents. From the perspective of promoting the appropriate use of natural resources and biodiversity, we have also recently focused on the manufacture and sale of gene-recombinant endotoxin-detecting reagents without the blood harvested from horseshoe crabs.
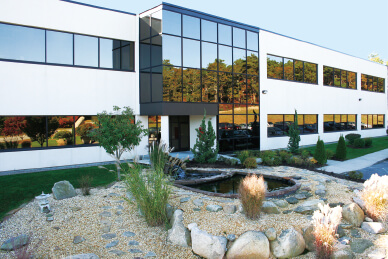
Dalton Chemical Laboratories, Inc., which became a Seikagaku subsidiary in March 2020, is a company that provides services including contract development and manufacturing (CDMO) services for pharmaceutical companies, such as manufacturing of chemical synthetics and pharmaceutical ingredients as well as manufacturing process development. Dalton was established in 1986 and has a U.S. and Canadian GMP*1–compliant manufacturing site for pharmaceuticals and other products in Ontario, Canada. Dalton currently has approximately 150 employees.
Seikagaku will utilize Dalton’s chemical synthesis technologies and expertise in manufacturing process development in its new drug development. In addition, Seikagaku will transfer the manufacturing of investigational drugs and some Seikagaku products to Dalton, as well as switch from the outsourced manufacturing of chemical synthetics used for research and other purposes to in-house production by Dalton.
*1 GMP: Good Manufacturing Practice
Standards for manufacturing control and quality control in manufacturing.
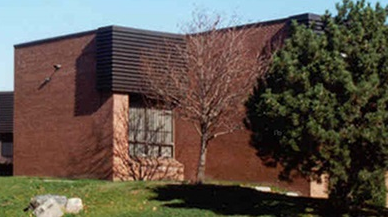